玻璃钢模具以其优异的性能和广泛的应用前景,在工业制造领域占据了重要地位。其制作过程较为复杂,但每一步都至关重要。本文将详细介绍玻璃钢模具的制作过程,帮助读者深入了解这一技术。
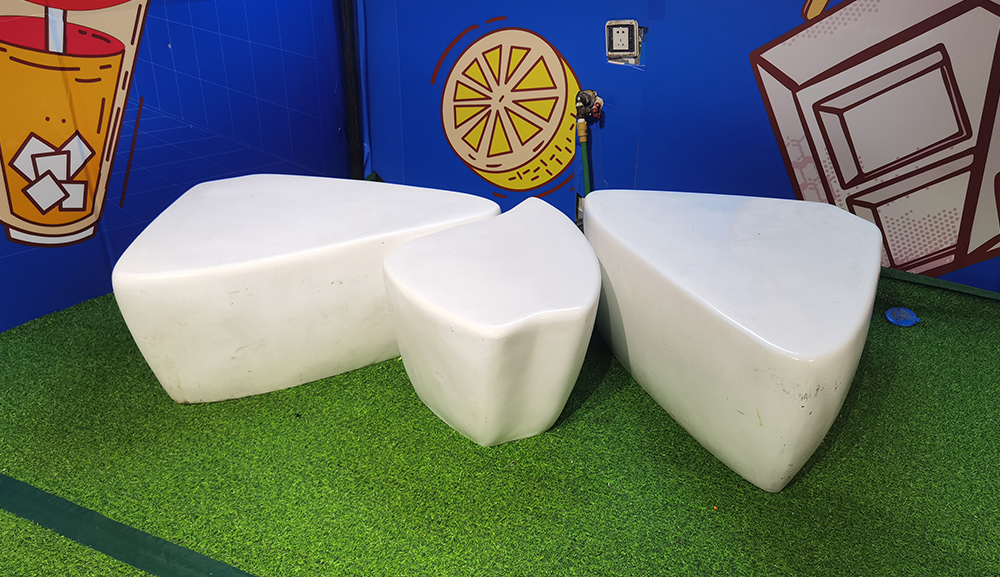
首先,制作玻璃钢模具的第一步是设计模具。设计阶段需要根据产品的要求和功能来确定模具的尺寸、形状和结构。设计师通常使用计算机辅助设计(CAD)软件进行详细的设计,以确保模具的各项参数准确无误。设计图纸完成后,需要进行工程评审,确保所有细节符合要求,并能有效实现生产目标。
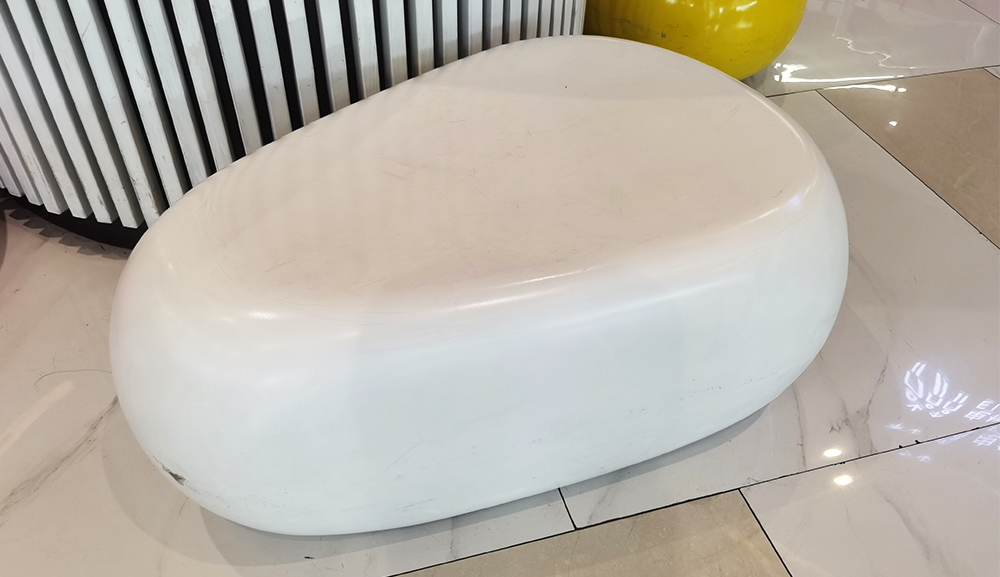
接下来是制作模具的原型。原型通常由木材、塑料或金属制成,作为最终模具的基础。制作原型时,要特别注意其表面光滑度和细节精确度,因为这将直接影响到后续玻璃钢模具的质量。原型制作完成后,会进行表面处理,以确保其能为后续的玻璃钢层提供良好的粘附基础。 第三步是进行模具的表面处理。为了使玻璃钢能更好地粘附在原型上,原型表面需要进行处理。常见的方法包括喷涂脱模剂和打磨表面。脱模剂可以防止玻璃钢在固化后与原型粘连,从而确保模具的顺利脱模。表面打磨则可以去除原型上的瑕疵,使其表面光滑平整。
然后,进入玻璃钢层的制作阶段。首先需要准备玻璃纤维和树脂。玻璃纤维通常为无碱纤维或短切纤维,与树脂混合后可以形成坚固的复合材料。制作时,树脂与硬化剂按一定比例混合后涂覆在原型表面,形成基底层。接着,铺设一层玻璃纤维布,再涂覆一层树脂,以形成加强层。重复这一过程,直到达到所需的厚度和强度。
玻璃钢层的固化是关键环节。通常情况下,模具会在一定的温度和湿度条件下进行固化,以确保玻璃钢材料的最佳性能。固化时间根据树脂的类型和环境条件不同而有所变化,一般需要几小时到数天不等。固化完成后,模具表面会变得坚硬且稳定,能够承受较大的机械应力。
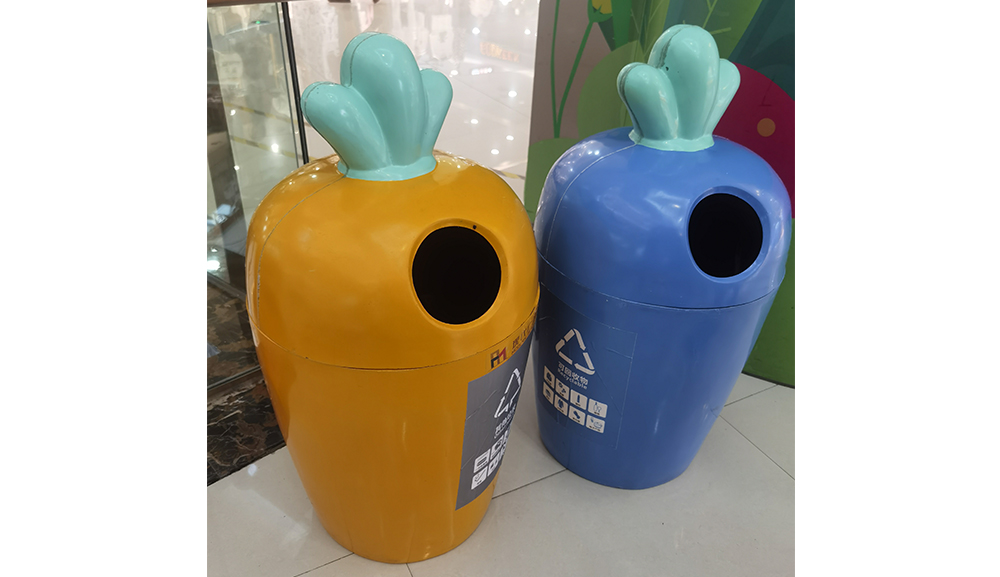